Wrestling with the infrastructure
With my son off at his moms, I had a grownup day, and I was all set to make some parts, make some progress on the plane. Instead, along with doing the laundary and ironing labels in the Wee Bairn's clothes, I wrestled with the Infrastructure.
I like overhead cord reels to manage the power in my shop, and I've got two of them. One of them is a US made job that hangs from the ceiling, is all metal, and costs a lot. In an idle moment, I bought another one from Harbor Freight, plastic, half the price, but I actually liked it better, at first, because it came with a longer "short cord" (the one you plug into the wall) and it had a better wall mount bracket.
Well, last week, it wouldn't retract. Harbor Freight doesn't fix ANYTHING, and it was out of warranty. I had the manual, with an exploded diagram, and it looked tricky - like it would fly apart as soon as I opened the cover. But I woke up this morning determined to fix this thing, and it wasn't THAT hard. Here was the problem, and the solution:
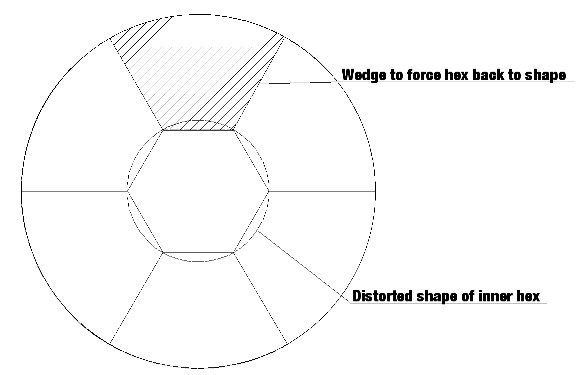
It's a bad design, frankly. The walls of the inner hex are molded plastic, about .060 in, if that, and they retain a formed steel hex, which in turn engages the spring that recoils the cord. A few hearty pulls, and the steel hex garps out the plastic hex, and you're all done. I had some fresh cookies of particle board from another project, so I bandsawed them into wedges, and jammed them in there. I used some urethane glue on the first few, then realized NOTHING sticks to polypropylene, and just wedged them in place dry. It was a little dodgey getting the reel, with the springs, the ratchet dog, etc., all back together, about 5.7, but we flailed only slightly.
It works now, and it only absorbed about an hour I would have preferred to spend building airplane parts.
The next challenge of the day was putting the foam on the air compressor enclosure. They sure shipped fast. I bought 3 linear feet of 4 feet wide 3/4" thick foam, with the adhesive back, and wished for more. I ended using a couple of acoustic panels salvaged from a Cubicle Farm, and piecing together scraps to finish the job.
My joinery was a bit off, and I had to rebuild the outer box, and it's still a bit tighter than I might like. If you do this, measure the machinery all around, add 3/4 inch clearance all around, add the thickness of the absorbtive material you plan to use - that's sum is now the INSIDE dimensions of your innermost box. Add the thickness of the box, the OUTSIDE layer of foam, 3/4 inches of clearance all around, the foam INSIDE the OUTSIDE box - now you've got the INSIDE dimensions of the OUTSIDE box.
You may recall we started at at 83 dB 6 feet away. Enclosing this puppy brought it down to 72dB, and adding the absorptive foam, inside and outside of the inner box, and inside the outer box, brought it down to about 63 dB. Now I just have to finish plumbing the thing....I'm using copper tubing and compression fittings. If it's good enough for water pressure (typically 80 psi around here) it should be good for 100 psi air. I know the tubing is good for it; we'll see about the fittings.
That sucked up the rest of the day. Girlfriend came over. It was time to cook dinner and/or make out, but I was in a nasty funk, having worked hard all day on nothing I WANTED to be working on. Then I burned the eggplant I was baking.
We went out to eat, again. I'm better now. Really. And I've got Sunday to get something done.
Labels: Project
0 Comments:
Post a Comment
<< Home