Mal Raff is a flight instructor with California Airways in Hayward, California. I've flown out of this FBO for about 5 years, never flown before Saturday with Mal. I've flown with some pretty good pilots, some good instructors, but Mal gave me one of the best lessons I've had in a small plane.
I've learned that instructors have teaching styles, and they may differ markedly from the student's learning style. The secret is to getting the most out of a given experience is to adapt - your learning style needs to yield, in the moment. After the flight, evaluate, and change if change is needed, but in the air, deal. Plus, it's always a crap shoot with a new flight instructor, as the cockpit is the world's worst classroom to begin with - noisy, high stress - and pilots tend to have egos, and instructors, since they know ever so much more than you do - you get the picture. Plus I'm nearly 50, and Mal has a good 15 year lead on me. We rassled a little at first, on pre-flight procedures, but I agreed to listen to his points, and I made mine.
My intention - and I had one for this lesson - was to dial in my flare at landings, which as Mal reminded me, is the END of a chain of events that started, in this training scenario, when I advanced the throttle for the first takeoff.
MAL'S LAW: You cannot (consistently) make good landings from bad approaches
First Corollary: You can certainly make a bad landing from a good approach.
Before we turned on the Master, Mal made this little sketch. Let me walk you through it. Upwind is up, final is on the bottom. The assumptions are a Cessna 15X/17X, and the winds are light.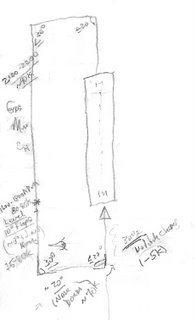
We've lifted off at about 55, and either released what LITTLE back pressure we might have been holding, or pushed the nose down a little, for as the plane accelerates, it tends to pitch up, and we want to climb out at about 75 kts. The turn from upwind to crosswind is made at least 200 ft AGL, and is SHALLOW, less than or equal to 20 degrees. Steep turns suck lift out of climb, and we'd prefer to gain altitude at this point rather than keep a super tight pattern.
Turn to Downwind may be a little steeper, as we are soon at Pattern Altitude, but less than 30 degreees. When we reach pattern altitude, we reduce power, to 2100-2200 RPM. Mal uses the G-M-C mnemonic, Gas (reach down and check the gas selector, should be BOTH for a Cessna), Mixture (full rich, push the center of the knob for a Cessna), and Carb heat (pull). You should be level, about 90 kts.
Abeam the numbers, time to reduce power again, to 1700-1800 RPM, and let the speed bleed off a little before lowering the flaps, AND putting the nose about 3 degrees below the horizon. 75 - 80 kts and descending should be the result. Approaching 45 degrees from the end of the runway, look out the left window and chose a spot on the horizon (or at least far enough away to reduce parallax to a minimum) 90 degrees from the downwind leg.
Turn to base should be spot on 30 degrees. You want to get it done, but not generate an accelerated stall. 30 degrees, watch your speed. Your "spot" will appear in the windscreen, roll out. On base, drop more flaps, to 20 degrees. Watch your speed. Start a shallow, less than or at most, equal to 20 degree bank to bring you to final. Once on the centerline, drop more flaps, WITHOUT CHANGING PITCH, and you should slow right down to 65 kts. Assess your glide path, and reduce the throttle to suit, closing it completely when you have the runway made. KEEP YOUR HAND ON THE THROTTLE: shit happens.
Ideally, the roundoff and flare should be a continuous function, starting sometime before reaching the runway threshold. In practice, it's more of a step function; increase back pressure, wait and see, pull a little more, wait, pull a little more, until you kiss the runway with the yoke all the way back, and a few little chirps of the tires. KEEP THE BACK PRESSURE ON until the nose wheel drops of it's own accord. DO NOT try and look over the nose, watch the edges of the runway with your peripheral vision.
I hadn't flown in 5 months, and have flown less than 20 hours in the last 3 years. After an hour on the Hobbs, following this mantra, and with a little coaching, I was earning the praise of a man from whom praise meant something.
None of this should be new to anyone who has read Stick and Rudder, still the best book on the actual motor skills and conceptual processing of flying. "Spotting" the base turn was an Ah Ha moment for me, and reminded me of learning to pirouette in ballet class about 25 years ago.
Labels: aviation